Canadian University Startup Makes Rare Earth-Free Electric Motors
Gallery
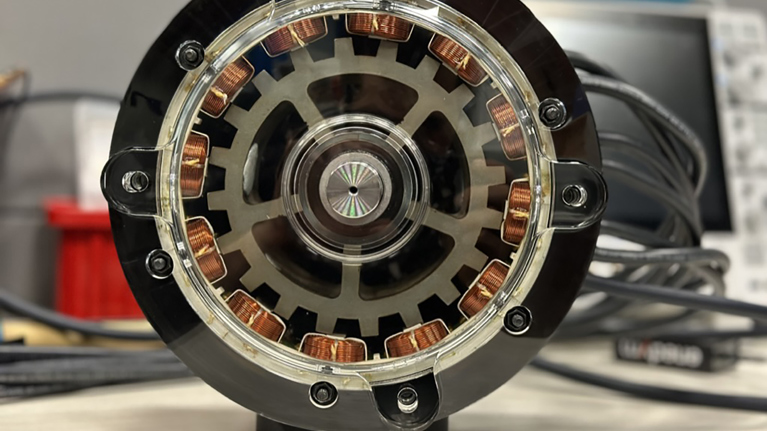


Much of the attention on electric vehicles (EVs) is currently centred on battery technology and range. Solid-state batteries provide an answer to most of the issues that plague today’s EVs, but they are still a few years away from being viable for mass production.
Batteries are important, but motors are just as crucial to an electric car. They are the engine of an EV and its only source of propulsion. Most new EVs today are equipped with one or more electric motors that use permanent magnets in their construction. Permanent magnet motors are quieter, more efficient, and provide greater torque at low speeds than alternative technologies. They are an easy choice for automakers, but permanent magnets are made with rare earth metals, which poses some issues, according to Dr. Ali Emadi, CEO and founder of Enedym, a McMaster University-based startup specializing in rare earth-free electric motors.
The Problems with Rare Earths

“Over 84 per cent of the global supply of rare earths are mined in China,” he says. “[Rare earth metals] have become a critical part of the global supply chain.” With ongoing trade wars and economic uncertainty, we need to reduce our dependence on China, which recently introduced export controls “weaponizing” rare earth metals, according to CSIS. Extracting rare earth metals from the ground also has a devastating impact on the environment and is an unsustainable practice, but global demand for them only continues to rise.
Innovation is needed, and Emadi says the motors his company produces are as efficient and powerful as permanent magnet motors. They’re also much cheaper to make. “Forty to 50 per cent of the cost of a [permanent magnet] propulsion motor is in the magnets, and our motors don’t have them,” he says.
Major automakers, including Jaguar, General Motors, and Tesla, are developing rare earth-free electric motors, but this Canadian startup, which is still a small operation of just 30 employees, says its Switch Reluctance Motors (SRM) are already being tested in the real world.
The company transplanted one of its motors into a Cadillac Lyriq for a GM-sponsored student-run competition called EcoCAR, a four-year challenge among 15 universities across North America. The goal is to develop the next generation of electric cars. Enedym also has prototype luggage tow tractors in action at Hamilton airport, part of a collaboration with Toyota.

How Does it Work?
Electric motors have just one moving part, called a rotor. The rotor sits inside a stationary housing called a stator. The stator is jam-packed with loops of copper windings that generate a magnetic field when current is applied. The magnetic field spins the rotor, which creates the electric motor’s torque output. Permanent magnet motors generate a magnetic field without a current being applied to the stator, making them more efficient, but Enedym’s magnet-free motor connects the copper windings in the stator directly to the power electronics with solid-state switches. Each winding gets switched on and off in sequence, causing the nearest rotor pole to align with the nearest energized winding, making it spin.
The Software Issue
“Our motors are very simple, but software and control for them is amazingly complex, but you only do the software once and then mass manufacturing takes over,” Emadi says.
He says it can take a company more than nine months to develop a motor and the software that controls it. There are electromagnetic engineers, thermal engineers, mechanical engineers, electrical engineers, and the list goes on. Each team works sequentially, and it can cost a company billions of dollars to fund this development. They recoup that cost by producing hundreds of thousands of motors, but Enedym works differently. The company has developed a comprehensive software platform that greatly accelerates the design process.
“Other [companies] take six to nine months to develop a motor. We do it in a week or two. It’s mind-boggling,” says Emadi.

The software took over 10 years to develop at McMaster, and it’s a multi-physics, multi-domain, AI-enabled tool that can be used to design motors comprehensively and optimize them for production. “We give the engineers better tools to design, develop, and optimize much faster,” says Emadi.
This design speed lets Enedym go after multiple domains, not just automotive. The company is working on wind-pitch motors that adjust the angle of the blades on windmills, and electric scooter motors for a large OEM.
The McMaster Automotive Resource Centre (MARC) in Hamilton, where Enedym is based, is also home to the facility for advanced rapid manufacturing (FARM). This is Enedym’s rapid prototyping facility, where it can work on designing motors for many different applications and produce them, albeit on a smaller scale than bigger motor companies. The key difference is that they can produce many different types of motors, but at a smaller volume, tackling multiple industries rather than producing hundreds of thousands of motors of a single design for one application. This flexibility and ability to quickly pivot to different domains is especially important today when tariffs seriously threaten North America’s auto industry.
“Electric motors are everywhere. It’s a massive market,” says Emadi. “They are the beating heart of anything that moves with electricity.”